Home > Products > Laser Micrometers > Triton™ Triple-Axis Scanning Laser Micrometers
Triton™ Triple-Axis Scanning Laser Micrometers
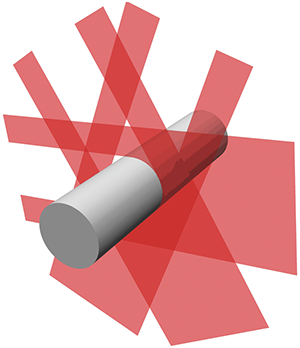
Triple-Axis Measurement
Resources
Accessories including roller guides, stands, calibration kits, window guards, and air purges
Product safety standards (e.g. CE, UL)
Triple-axis (also called triple-plane) models make measurements from three viewpoints. The three axes of measurement are coplanar and separated by 60 degrees from each other. The product to measure is perpendicular to the measurement field. (See the associated image.) Typically, the micrometer is used to measure product diameter, ovality, and position. To see illustrations and explanations of these and other common measurement types available with Triton™ triple-axis scanning laser micrometers, visit the Measurements page.
For round products, three axes of inspection offer the best average diameter and an accurate measure of ovality, also called roundness or eccentricity
Ovality
Eccentricity is sometimes used as a measure of the degree to which two forms share a common center, as in an insulated wire where the core (the wire) and the outer insulation do not share the same center. However, LaserLinc uses these terms to refer to a measure of how well the measured product conforms to a circle. LaserLinc uses the term concentricity as a measure of the degree to which two forms share a common center..
If the ovality of your product must meet a defined specification, then a LaserLinc Triton-series micrometer is the product you require. LaserLinc’s Triton technology provides an accurate measure of ovality regardless of product orientation. (See accompanying graph to the right.)
If checking for defects, a Triton micrometer is especially effective at identifying small defects that do not encircle the product.
A common application for Triton micrometers is measurement of medical tubing, especially catheters.
For benchtop applications, a Triton micrometer is perfect for inspecting the product without rotating it, saving time without sacrificing accuracy.
Model Overview
The Triton312 and Triton330 micrometers offer the advantages of three-axis measurement in a very compact package with exceptional accuracy. The Triton331™ and Triton360™ models add a fast measurement rate and with the 360, up to a two inch [50.8 mm] measurement range. For in-process measurement of non-round profiles, products with varying diameter, and flaw detection applications, the latter models can be upgraded to the fastest measurement rates of any scanning laser micrometer: 4,000 Hz per axis (12,000 Hz aggregate). For discrete part measurement, a higher measurement rate facilitates faster inspection cycle times.
Triple-axis models share the following characteristics:
-
Measure any material, even clear and translucent products (glass logic
Glass Logic
Glass Logic uses specially designed hardware and software to properly measure objects even when laser light bleeds through them. Without this logic, unexpected bleed-thru would be treated as extra parts or debris in the measurement field and prevent a measurement from being made. This feature is included at no cost with all LaserLinc interfaces. is a software option included at no charge with all systems) - Use in-process or for benchtop/offline applications
- Measurement accuracy and micrometer operation are unaffected by line speed
- Mount in any orientation
- Multiple mounting surfaces with precision locating holes for flexible mounting, but also for flexible attachment of accessories
- Choose from four different models
- Can be used with the Total Vu™ HMI for complete product and process monitoring, reporting, and control
- Can be used with a SmartLinc™ processor for an intelligent interface via industrial communication protocols
- Available with Ethernet-based NetLinc™ signal interface
- Mounting adapters are available to deploy effective six-axis measurement for superior flaw detection and average diameter accuracy
Four-Year Warranty!
The robust design of LaserLinc laser micrometers ensures reliable operation in harsh manufacturing environments. All are covered by an industry-leading FOUR-YEAR warranty that covers all parts and labor. For warranty details, including LaserLinc’s “spare-in-the-air” replacement offer, visit the Warranty and Service page.
Notable applications include:
- Extruded products such as insulated wire, cable, hose, pipe, and tubing
- Average diameter and ovality of synthetic cork for wine bottles
- Taper tube / Bump tube
- Flaw detection
The matrix below shows triple-axis models by measurement range and measurement rate. Triton model numbers begin with 3 (the number of axes of measurement), followed by the approximate gate size (in millimeters).
Click on a model number in the Model column to access its specifications and drawings.
Inches |
Metric (mm) |
Measurement Rate (Hz)1 |
||||
Model |
Minimum Part Size |
Maximum Part Size |
Minimum Part Size |
Maximum Part Size |
Standard |
Options |
.004 |
.45 |
.102 |
11.4 |
600 / 1800 |
||
.004 |
1.15 |
.102 |
29.2 |
300 / 900 |
||
.01 |
1.07 |
.254 |
27.2 |
1,600 / 4,800 |
4,000 / 12,000 |
|
.016 |
2.07 |
.406 |
52.6 |
1,600 / 4,800 |
4,000 / 12,000 |
1Measurement rate is the number of times per second each measurement field (or axis) is scanned. The number after the slash is the aggregate measurement rate for all three axes.